Unraveling the Intricacies of Glazing: A Comprehensive Exploration of Glazing Techniques


Latest Technological Innovations
In the realm of glazing techniques, the latest technological innovations have begun to revolutionize traditional practices. Artists and professionals now have access to cutting-edge advancements that streamline the glazing process and enhance creative possibilities. From precision application systems to automated kilns with intricate control mechanisms, these technologies are reshaping the way glazing is approached. The integration of digital tools for glaze formulation and application has opened up new avenues for experimentation and customization, pushing the boundaries of what is achievable in the world of ceramics.
Startup Spotlight
While glazing may seem deeply rooted in tradition, startup ventures have entered the scene with innovative approaches to this age-old craft. One such startup company, Glaze Fusion, has garnered attention for its revolutionary glaze application device that combines precision engineering with artistic flair. Founded by a team of passionate ceramic artists and tech experts, GlazeFusion embarked on a journey to disrupt the glazing industry. Despite facing initial skepticism and logistical challenges, the startup's commitment to product refinement and customer feedback paved the way for its success story. Through strategic partnerships and a dedication to quality, GlazeFusion overcame market obstacles and established a unique position in the competitive landscape.
Tech Industry Trends
In the ever-evolving landscape of glazing techniques, several key trends are shaping the industry's direction. A surge in demand for eco-friendly glazes has spurred companies to develop sustainable, non-toxic formulations that align with contemporary environmental consciousness. Additionally, the rise of multi-media integration in glazing has led to collaborations between ceramic artists and digital designers, resulting in stunning visual effects and textured surfaces. As technology continues to intersect with artistic expression, the boundaries between traditional and digital glazing methods blur, offering a world of possibilities for creators and consumers alike.
Investment Opportunities
With the growing interest in artisanal crafts and personalized aesthetics, investment opportunities in the glazing sector are on the rise. Venture capitalists and angel investors are increasingly drawn to startups that offer disruptive solutions in glaze formulation, application, and artistic innovation. Factors such as market demand, scalability of products, and differentiation from existing offerings play a pivotal role in assessing the investment potential of glazing ventures. Promising startups in the glazing space present unique value propositions that cater to niche markets or address emerging trends, attracting capital infusion from forward-thinking investors seeking high returns in the rapidly evolving craft industry.
Entrepreneurship Insights
For aspiring entrepreneurs looking to venture into the world of glazing techniques, navigating the complexities of a competitive market requires strategic foresight and creative instinct. Understanding consumer preferences, market gaps, and technological advancements is crucial in establishing a successful glazing business. Entrepreneurs can benefit from leveraging digital marketing tools, packaging their products with compelling storytelling, and emphasizing the artisanal craftsmanship behind their creations. By staying agile, adapting to industry trends, and fostering a strong network within the creative community, entrepreneurs in the glazing sphere can carve out a distinctive brand identity and thrive in an ever-expanding market landscape.
Introduction to Glazing:
Glazing is an indispensable aspect that plays a pivotal role in the world of artistry, particularly in ceramics and pottery. This section serves as the foundational groundwork for understanding the nuances and intricacies of glazing techniques. By delving into the basics of glazing, enthusiasts and professionals alike can grasp the essence of this art form. From the historical significance of glazing to the innovative applications in modern times, this section aims to shed light on the essential principles that underpin the enchanting world of glazing.
Understanding the Basics:
What is Glazing?
Glazing, in essence, is an art form that involves applying a vitreous substance to ceramics before firing to create a durable, decorative finish. The core characteristic of glazing lies in its ability to enhance the aesthetic appeal of pottery while providing a protective coating. Its versatility and adaptability make it a popular choice among artists and craftsmen. Despite its benefits, glazing also presents challenges such as achieving consistency in application and navigating the complexities of different types of glazes.
Historical Significance of Glazing
The historical significance of glazing traces back centuries, characterized by its role in both art and functionality. Ancient civilizations utilized glazing not only to adorn their pottery but also to waterproof and preserve vessels for daily use. The evolution of glazing techniques over time reflects cultural shifts and technological advancements, marking a transformative journey of artistic expression and utilitarian purpose.
Importance of Glazing:
Enhancing Aesthetics:
Enhancing aesthetics is a central aspect of glazing, where artists leverage different colors, textures, and finishes to elevate the visual appeal of their creations. Glazing offers a vast canvas for creative expression, enabling artists to experiment with various techniques and styles to achieve desired artistic outcomes. The amalgamation of science and art in glazing underscores its significance in the realm of ceramics and pottery.
Protective Qualities of Glazing:
Beyond aesthetics, glazing serves a dual purpose by providing a protective layer that enhances the durability and longevity of ceramic pieces. The chemical composition of glazes can offer resistance against stains, scratches, and external elements, ensuring that the artwork remains pristine and resilient. This protective trait amplifies the value of glazing in preserving and safeguarding artistic creations.
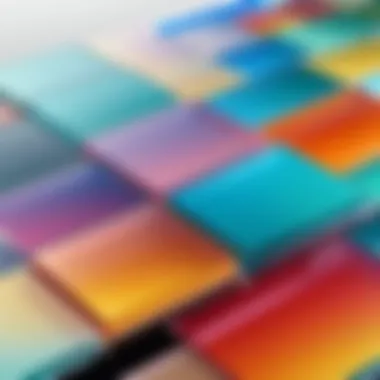
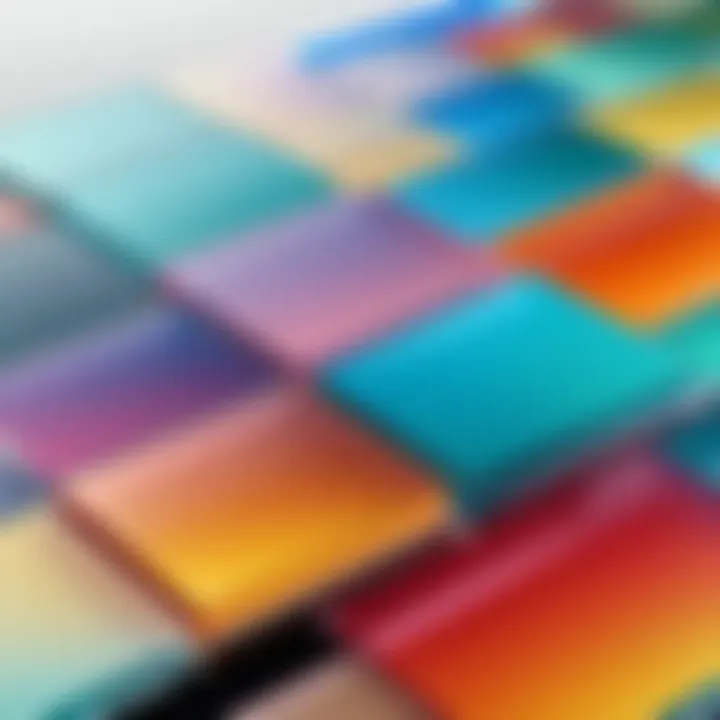
Types of Glazes:
Transparent Glazes:
Transparent glazes, known for their clarity and luminosity, are favored for showcasing the natural beauty of ceramics. These glazes allow underlying colors and textures to shine through, adding depth and richness to the finished piece. Artists appreciate transparent glazes for their ability to accentuate intricate details and create a glossy, glass-like surface.
Opaque Glazes:
In contrast to transparent glazes, opaque glazes exhibit a solid and non-transparent appearance, offering a range of vivid colors and matte finishes. Opaque glazes are ideal for concealing imperfections or achieving bold color contrasts on pottery. Artists often utilize opaque glazes for decorative purposes and to enhance visual impact.
Crystalline Glazes:
Crystalline glazes feature intricate crystalline formations that develop during the firing process, resulting in unique patterns and textures on ceramics. The crystalline effect adds a touch of sophistication and allure to glazed pieces, creating a mesmerizing visual display. Crafting with crystalline glazes requires skill and precision to control the crystal growth and achieve desired aesthetics.
Composition of Glazes
In the realm of ceramics, the composition of glazes stands as a vital pillar underlying the entire creative process. Understanding the intricate balance of key components, colorants, and firing techniques is crucial for any artisan looking to delve into the world of glazing techniques. From enhancing aesthetic appeal to providing protective qualities, every aspect of glaze composition plays a significant role in the final outcome of a ceramic piece. This section will delve deep into the essential elements that constitute glazes, shedding light on their importance and impact on the artistry of ceramics.
Key Components
Silica
Silica, a fundamental component of glazes, boasts exceptional heat-resistance properties, making it a popular choice in ceramic arts. Its key characteristic lies in its ability to contribute to the glass-forming process, enhancing the durability and smooth texture of the glazed surface. Despite its numerous advantages, silica does possess a tendency to form crystalline structures at high temperatures, which can sometimes lead to surface irregularities. Understanding the nuances of silica's behavior during firing is imperative for achieving desired glaze effects.
Fluxes
Fluxes play a pivotal role in lowering the melting point of glaze components, facilitating the melting and bonding process during firing. The key characteristic of fluxes lies in their ability to promote the flow of glazes, ensuring even coverage and adhesion to the ceramic surface. While fluxes are indispensable for achieving desired glaze textures and finishes, an excessive amount can lead to glaze running off the surface, causing defects. Balancing the proportion of fluxes is essential for controlling the viscosity and stability of the glaze mixture.
Stabilizers
Stabilizers act as agents that enhance the overall consistency and viscosity of glazes, preventing unwanted settling of particles during storage and application. Their key characteristic lies in their ability to maintain the homogeneity of the glaze mixture, ensuring uniform coating and adhesion. Despite their crucial role in glaze formulation, stabilizers can sometimes lead to over-viscosity, impeding the flow and application of glazes. Careful consideration of stabilizer types and proportions is necessary for achieving optimal glaze performance.
Colorants and Additives
Metal Oxides
Metal oxides serve as common colorants in glazes, imparting vibrant hues and shades to ceramic surfaces. Their key characteristic lies in their ability to produce stable colors under varying firing conditions, enhancing the aesthetic appeal of glazed ceramics. While metal oxides offer a wide range of color options, certain oxides can exhibit toxicity concerns during processing, requiring careful handling and control. Understanding the unique color properties of metal oxides is essential for achieving consistent and desired glaze outcomes.
Opacifiers
Opacifiers play a crucial role in modifying the translucency of glazes, creating opaque or semi-opaque finishes on ceramic surfaces. Their key characteristic lies in their ability to scatter light and create matte or satin effects, adding depth and visual interest to glazed pieces. Despite their decorative advantages, opacifiers can sometimes alter the flow and application behavior of glazes, necessitating meticulous testing and adjustment. Selecting the right opacifier based on desired opacity levels is paramount for achieving the intended aesthetic results.
Firing Techniques
Oxidation vs. Reduction Firing
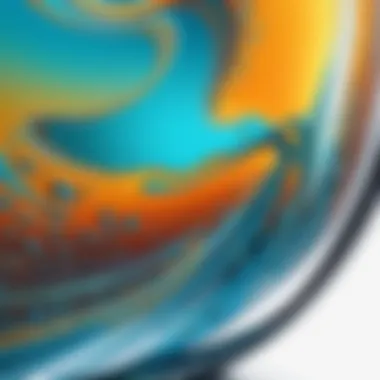
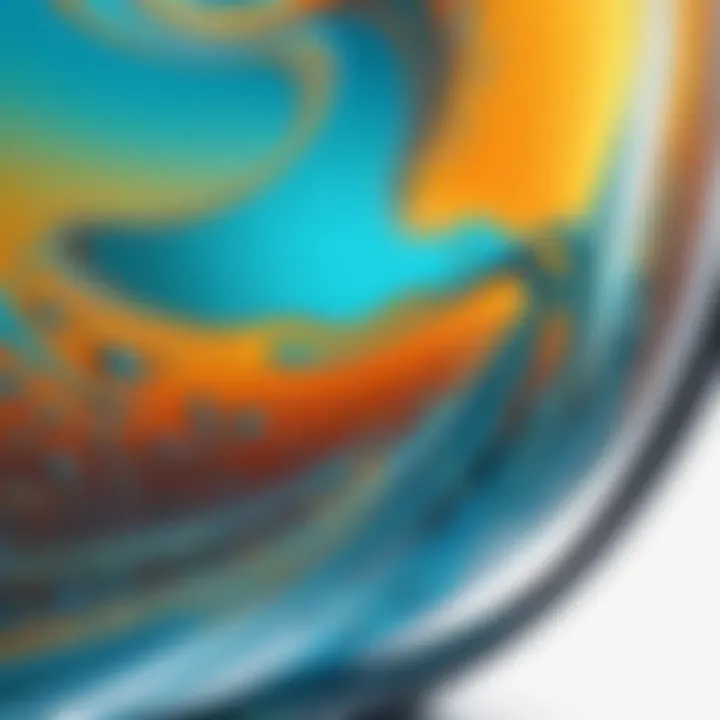
The choice between oxidation and reduction firing techniques significantly influences the final appearance and properties of glazed ceramics. Oxidation firing, characterized by ample oxygen presence in the kiln atmosphere, promotes vibrant colors and glossy finishes in glazes. In contrast, reduction firing, with limited oxygen availability, tends to produce unique color variations and surface effects due to the alteration of metal oxides. Understanding the impact of oxidation and reduction atmospheres on glaze chemistry is essential for achieving desired color development and surface textures.
Atmospheric Conditions
Atmospheric conditions within the kiln play a critical role in determining the success of firing techniques and glaze effects. Controlling factors like temperature gradients, airflow, and humidity levels can significantly impact the outcome of glazed ceramics. Maintaining a consistent and well-regulated atmosphere during firing operations is essential for achieving even heat distribution and minimizing potential defects. Modulating atmospheric conditions according to specific glaze requirements is paramount for ensuring optimal firing results and realizing the artistic vision behind the glazing process.
Application Methods
In this section, we delve into the crucial aspect of Application Methods within the realm of glazing techniques. Application Methods are pivotal in determining the final outcome and quality of glazed products. By understanding the specific elements and considerations related to Application Methods, enthusiasts and professionals gain valuable insights into enhancing their glazing endeavors. Techniques such as brushing, dipping, pouring, spraying, and airbrushing play a vital role in the glazing process, impacting aesthetics and functionality.
Brushing Techniques
Layering
Layering in glazing involves applying multiple coats of glaze to achieve depth, complexity, and richness in color. The key characteristic of Layering lies in its ability to create nuanced visual effects, adding depth and dimension to the surface of the ceramic or pottery. Artists often opt for Layering as it allows for the gradual buildup of color and texture, leading to intricate and captivating results. While Layering enhances the visual appeal of glazed pieces, artists must also be mindful of potential inconsistencies or uneven application that may arise.
Detailing
Detailing is a meticulous aspect of glazing where intricate patterns, designs, or textures are added to the surface of ceramic or pottery. The key characteristic of Detailing is its ability to enhance the overall aesthetics and intricacy of the glazed piece, adding a personalized touch and visual interest. Artists favor Detailing for its capacity to elevate the visual impact of glaze, making each piece unique and engaging. However, Detailing requires precision and attention to ensure consistent application and avoid potential smudges or imperfections.
Dipping and Pouring
Uniform Coating
Uniform Coating entails immersing the ceramic or pottery into a glaze solution to achieve an even and consistent finish. The key characteristic of Uniform Coating is its ability to provide a seamless coating across the entire surface, ensuring uniformity in color and texture. This technique is favored for its efficiency and practicality, especially when working with larger pieces or mass production. While Uniform Coating streamlines the glazing process, artists must control the dipping time and thickness of the glaze to prevent drips or runs that may result in blemishes.
Drip Effects
Drip Effects involve allowing excess glaze to drip or flow on the surface of ceramic or pottery, creating organic patterns or textures. The key characteristic of Drip Effects is their unpredictable and spontaneous nature, adding a sense of dynamism and originality to the glazed piece. Artists appreciate Drip Effects for their ability to introduce a playful or unconventional element to the glaze application, resulting in unique and visually stimulating outcomes. However, managing Drip Effects requires skill and timing to achieve the desired aesthetic without compromising the overall integrity of the piece.
Spraying and Airbrushing
Precision Application
Precision Application refers to the controlled spraying of glaze onto ceramic or pottery surfaces to achieve accuracy and detail. The key characteristic of Precision Application is its ability to target specific areas with finesse, creating sharp lines, gradients, or intricate patterns. This technique is valued for its ability to achieve intricate details and gradual color transitions with precision. While Precision Application offers versatility and control in glaze application, artists must practice control and consistency to avoid oversaturation or uneven coverage that may detract from the final result.
Gradient Effects
Gradient Effects in glazing involve creating smooth transitions between colors or hues using an airbrush or spray gun. The key characteristic of Gradient Effects is their ability to achieve soft, blended color transitions that enhance the visual appeal of the glazed piece. Artists often utilize Gradient Effects to add depth, dimension, and visual interest to their creations, showcasing a seamless fusion of colors. However, mastering Gradient Effects requires a skilled hand and understanding of color combinations to achieve harmonious gradients without abrupt shifts in hue.
Specialized Glazing Techniques
Specialized glazing techniques play a pivotal role in the world of glazing, offering craftsmen and artisans unique avenues to express their creativity and skills. These techniques, such as Majolica, Raku Firing, and Salt Glazing, bring distinctive characteristics and effects to glazed surfaces, elevating them from traditional forms to exceptional works of art. Enthusiasts and professionals in the field of ceramics and pottery are increasingly drawn to these specialized techniques for their ability to add depth, texture, and visual interest to their creations. Understanding and mastering these techniques require not only technical proficiency but also a keen artistic sensibility to achieve desired results that captivate viewers.
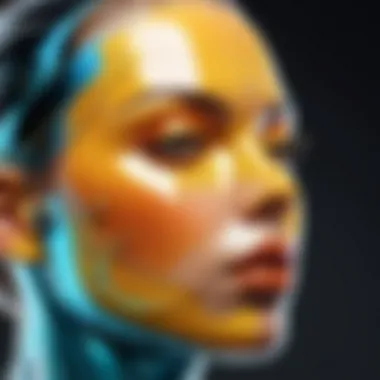
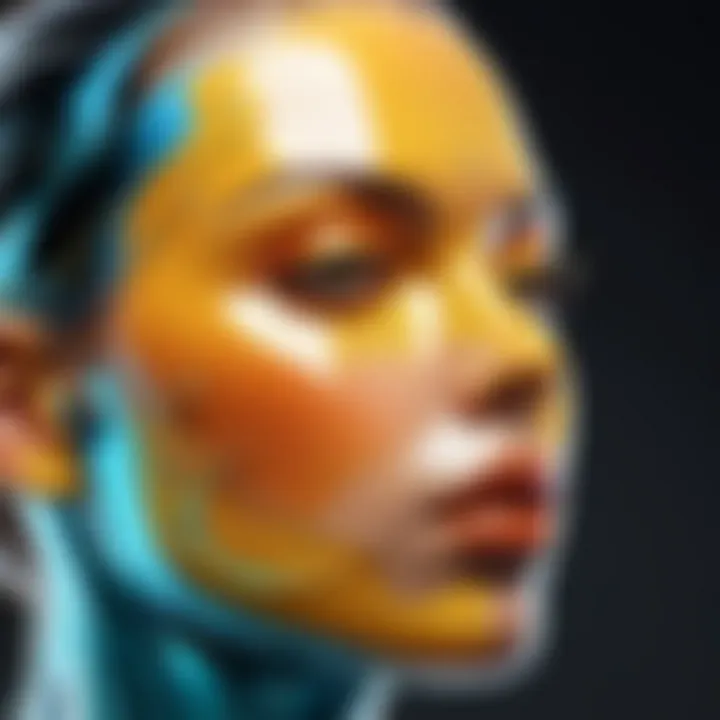
Majolica
Majolica, a celebrated glazing technique originating from the Italian Renaissance period, encompasses a range of decorative methods that involve applying colorful, opaque glazes to ceramics. Within the realm of Majolica, Tin-Glazing stands out as a significant aspect that imparts a lustrous, creamy white finish to the pottery, enhancing the vibrancy of colors and intricate designs. This technique's characteristic white base serves as a canvas for vivid decorative patterns, bringing a timeless elegance to ceramics. Craftsmen appreciate Tin-Glazing for its ability to create a smooth surface that supports detailed brushwork and intricate motifs, making it a preferred choice for artists looking to achieve refined and sophisticated pieces. However, Tin-Glazing requires precise application and control during the firing process to prevent potential imperfections or inconsistencies, adding a layer of complexity that demands skill and precision.
Decorative Patterns in Majolica demonstrate the artistic versatility and creativity inherent in this glazing technique. Artists and potters use decorative patterns to embellish ceramics with ornate motifs, botanical designs, geometric shapes, and narrative scenes, infusing each piece with personalized storytelling and visual appeal. The intricate detailing and precise execution of these patterns elevate the aesthetic value of the artwork, showcasing the artisan's mastery of Majolica techniques. While Decorative Patterns offer endless possibilities for artistic expression and customization, artists must balance creativity with technical expertise to achieve harmonious and captivating compositions that resonate with audiences.
Raku Firing
Raku Firing, an ancient Japanese firing technique revered for its unpredictable and dramatic outcomes, adds an element of spontaneity and experimentation to the glazing process. One distinctive aspect of Raku Firing is its incorporation of Smoke Effects, where the ceramics are exposed to open flames and smoking materials during the firing, resulting in mesmerizing patterns and colors that reflect the natural elements at play. The dynamic interplay of fire and smoke imbues Raku-fired pieces with a sense of vitality and raw beauty, capturing the essence of creation through elemental forces. Artists are drawn to Smoke Effects for their ability to introduce organic, free-flowing patterns that evoke a sense of primal energy and movement, creating visual intrigue and depth in the finished work.
Post-Firing Reduction is another crucial element in the Raku Firing process, contributing to the distinctive aesthetic qualities of Raku ceramics. This reduction phase involves placing the hot pottery in a reduction chamber or covering it with combustible materials to create an oxygen-deficient environment, resulting in unique surface textures and metallic luster. The reduction step transforms the surface of the ceramics, enhancing contrast, and depth through a play of light and shadow, adding a dynamic dimension to the finished artwork. While Post-Firing Reduction presents opportunities for creating striking visual effects and enriching the tactile experience of the pieces, artists must carefully monitor and control this stage to achieve desired outcomes without compromising the structural integrity of the ceramics.
Salt Glazing
Salt Glazing, a time-honored technique dating back to the medieval period, offers artists a method to introduce distinctive textures and finishes to pottery surfaces. The usage of Sodium Vapors during the firing process creates a unique orange-peel-like surface on the ceramics, resulting in a rugged and tactile quality that enhances the sensory experience for both the artist and the viewer. Sodium Vapors interact with the silica in the clay body, forming a glassy coating that fuses with the surface, creating a durable and aesthetically appealing finish that accentuates the form and contours of the pottery. Artists appreciate the unpredictability and organic nature of Salt Glazing, as each firing yields varying results, contributing to the allure of handcrafted and one-of-a-kind pieces.
Textural Finishes in Salt Glazing further enrich the tactile and visual aspects of the artwork, allowing artists to experiment with a myriad of surface treatments and sculptural effects. From rough, pitted surfaces to smooth, glossy finishes, Textural Finishes enable artists to infuse their creations with depth, character, and visual interest. The emphasis on textures in Salt Glazing not only enhances the aesthetic appeal of the ceramics but also provides a sensory dimension, inviting viewers to appreciate the artwork through touch and visual exploration. However, achieving desired Textural Finishes requires a nuanced understanding of clay behavior, firing atmospheres, and glaze compositions, as the interactions among these elements dictate the final appearance and feel of the finished pieces.
Advanced Glazing Innovations
In the realm of glazing techniques, one cannot overlook the pivotal role of Advanced Glazing Innovations. These cutting-edge advancements revolutionize the way we perceive and utilize glazes in modern applications. By delving deep into Advanced Glazing Innovations, we unearth a treasure trove of possibilities that elevate aesthetics and functionality to new heights. These innovations incorporate state-of-the-art technologies that propel traditional glazing practices into the future, catering to the discerning needs of artists, architects, and designers.
Nano-Coatings
Self-Cleaning Properties
Nano-coatings introduce a paradigm shift in glazing technology with their remarkable Self-Cleaning Properties. This innovative feature ensures that glazed surfaces repel dirt, grime, and water, maintaining a pristine appearance effortlessly. The key characteristic of Self-Cleaning Properties lies in their ability to break down organic residues upon exposure to light, a process known as photocatalysis. This not only enhances the longevity of glazed surfaces but also reduces the need for frequent cleaning, making it a sustainable choice for environments where cleanliness is paramount. Despite its advantages, some considerations include potential degradation over time and the necessity for adequate exposure to light for optimal performance, factors to weigh when considering Self-Cleaning Properties in glazing applications.
Anti-Reflective Surfaces
Another game-changer in the domain of Advanced Glazing Innovations is the integration of Anti-Reflective Surfaces. These surfaces effectively minimize glare and reflections, improving visibility and clarity for observers. The key characteristic of Anti-Reflective Surfaces lies in their ability to reduce light reflection through nanostructures that manipulate light waves, promoting better light transmission. This makes Anti-Reflective Surfaces an ideal choice for enhancing the visual appeal of glazed products in various settings. While the benefits of reduced glare are evident, challenges may include specialized production methods and higher costs associated with implementing Anti-Reflective Surfaces, factors that influence their adoption in glazing projects.
Electrochromic Glazing
Smart Glass Technology
Electrochromic Glazing introduces a futuristic dimension to glazing through its innovative Smart Glass Technology. This dynamic feature allows for adjustable transparency levels, giving users control over privacy, light filtration, and energy efficiency. The key characteristic of Smart Glass Technology lies in its responsiveness to external stimuli, enabling real-time modifications to suit changing environmental conditions or user preferences. This smart functionality makes Electrochromic Glazing a sought-after choice for modern architectural designs and smart living spaces. While the advantages of increased versatility and energy savings are significant, special considerations include potential system complexities and maintenance requirements that accompany Smart Glass Technology, aspects to ponder when integrating such solutions in glazing projects.
Privacy Control
Privacy Control emerges as a vital aspect of Electrochromic Glazing, offering unparalleled discretion and visual comfort. This feature allows users to switch between transparent and opaque states, maintaining privacy without compromising natural light levels. The key characteristic of Privacy Control lies in its ability to provide on-demand seclusion through tint adjustment, ensuring convenience and security in varied settings. The unique feature of Privacy Control enhances user experience by offering a customizable balance between transparency and privacy. Though the benefits of adaptable privacy solutions are evident, challenges may include potential electronic malfunctions or privacy mode restrictions, factors necessitating careful consideration when implementing Privacy Control in glazing projects.
Photovoltaic Glazes
Solar Energy Integration
Photovoltaic Glazes represent a remarkable synergy of aesthetics and sustainability through their Solar Energy Integration capabilities. These innovative glazes harness solar energy to generate electricity, transforming glazed surfaces into efficient energy sources. The key characteristic of Solar Energy Integration lies in its dual functionality, acting as both a decorative element and a renewable energy generator. This not only reduces carbon footprints but also contributes to energy cost savings, making Photovoltaic Glazes a green solution for architectural and design projects. Despite the advantages of eco-friendly energy production, practical considerations include installation complexities and upfront costs associated with integrating Solar Energy Integration, aspects to evaluate when opting for energy-efficient solutions in glazing applications.
Energy-Efficient Applications
Energy-Efficient Applications play a crucial role in the widespread adoption of Photovoltaic Glazes, focusing on sustainability and performance optimization. These applications aim to enhance energy conversion efficiency and maximize the usability of solar power generated through glazing systems. The key characteristic of Energy-Efficient Applications lies in their ability to fine-tune energy output and usage, ensuring optimal performance and resource utilization. This makes Energy-Efficient Applications a practical choice for projects seeking to achieve energy autonomy and reduce dependence on conventional power sources. While the benefits of energy savings and environmental impact reduction are substantial, challenges such as system maintenance and compatibility considerations may influence the decision-making process when incorporating Energy-Efficient Applications in glazing designs.