Exploring Ericsson's Smart Factory: Revolutionizing Manufacturing
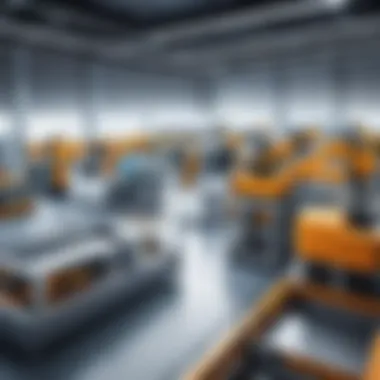
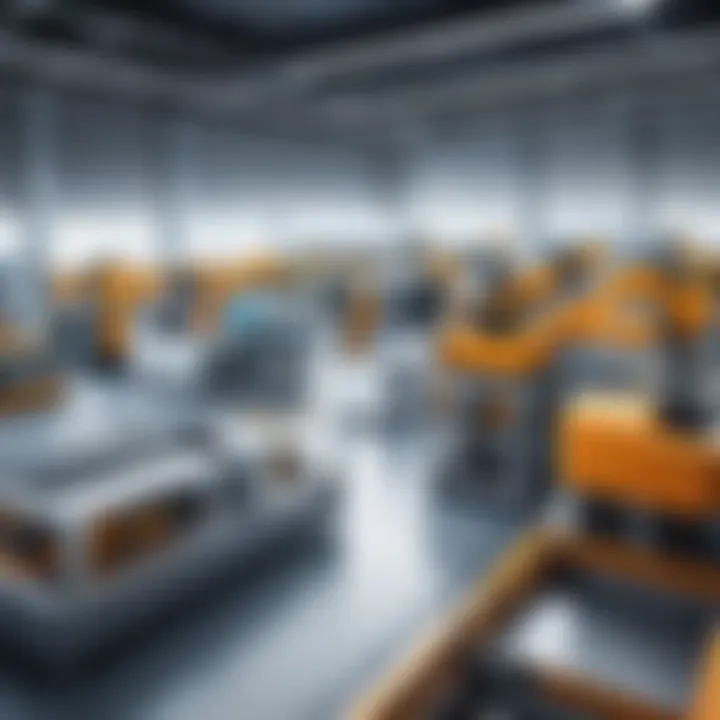
Intro
The manufacturing industry is undergoing a significant transformation, primarily fueled by the integration of advanced technologies. Among the leaders in this shift is Ericsson, a company that has embraced the concept of a smart factory. This article explores how Ericsson's innovative approach to manufacturing uses automation, artificial intelligence, and the Internet of Things to redefine efficiency and productivity in the sector. By analyzing these technologies, we can understand their implications not only for manufacturing processes but also for the workforce and sustainability efforts.
Latest Technological Innovations
Overview of the newest high-tech advancements
Ericsson's Smart Factory incorporates several cutting-edge technologies that are reshaping the traditional manufacturing landscape. The use of advanced automation allows for a more streamlined production process, eliminating many manual errors and inefficiencies. Artificial intelligence plays a crucial role, facilitating real-time data analysis and decision-making.
The Internet of Things connects machines and devices, providing invaluable data insights. This interconnectedness enables predictive maintenance, ensuring machines operate at optimal levels and reducing downtime.
Detailed analysis of futuristic technologies and their implications
Diving deeper into these technologies reveals their potential to dramatically alter the way manufacturing is approached. For instance, the integration of AI can lead to enhanced quality control, where machines can detect faults and correct them instantaneously. Moreover, this technology can adapt production lines to respond to changing demands without significant manual intervention.
In terms of sustainability, IoT devices can monitor energy usage and material consumption, paving the way for more eco-friendly practices. Reducing waste and optimizing resource consumption aligns with global sustainability efforts, an increasingly important consideration for modern enterprises.
"The future of manufacturing relies on the seamless integration of technology to enhance both efficiency and sustainability."
The Impact on Workforce Dynamics
As manufacturing processes shift toward greater automation, the role of the workforce is also evolving. Workers are now required to possess new skills that align more closely with technology management instead of manual labor.
This shift poses challenges and opportunities. On one hand, there is a risk of job displacement for roles that become automated. Conversely, it creates demand for skilled technicians and analysts who can manage advanced technologies. Companies must therefore invest in education and training initiatives to equip their workforce with the necessary tools to thrive in this changing landscape.
Sustainability Efforts
Ericsson’s Smart Factory initiative significantly contributes to sustainable manufacturing practices. By leveraging technology, the eco-footprint of manufacturing operations can be reduced. Streamlined production processes minimize waste while intelligent manufacturing techniques maximize resource efficiency.
Epilogue
The interplay of advanced automation, AI, and IoT technologies in Ericsson's Smart Factory offers valuable lessons for the future of manufacturing. These advancements hold the potential to redefine efficiency, reshape workforce dynamics, and drive sustainability efforts in the manufacturing sector. Organizations that can effectively adapt to these changes will not only survive but thrive in an increasingly competitive landscape.
Foreword to Smart Factories
The concept of smart factories represents a significant leap forward in the manufacturing industry. It relies on advanced technologies to automate processes, improve efficiency, and enhance overall productivity. This transformation is essential as businesses face increasing pressure to adapt to rapidly changing market demands. Smart factories promise not only to refine production mechanisms but also to create a more agile and responsive manufacturing environment.
A smart factory incorporates elements such as the Internet of Things (IoT), artificial intelligence (AI), and big data analytics. These technologies work together to create interconnected systems that allow for real-time insights and improved decision-making. By understanding these concepts, we can grasp how smart manufacturing holds the potential to revolutionize traditional factory models.
Defining Smart Manufacturing
Smart manufacturing is an integrated approach that leverages advanced technologies to enhance manufacturing processes. It focuses on agility and adaptability, allowing manufacturers to respond quickly to variations in demand. At its core, smart manufacturing entails:
- Data-Driven Decision Making: Collecting and analyzing data to optimize operations.
- Automation and Robotics: Using machines to perform repetitive tasks reduces human error and increases output.
- Real-Time Monitoring: Keeping track of production metrics to enable timely adjustments.
These elements combine to create a manufacturing ecosystem that is not just efficient but also sustainable.
The Evolution of Manufacturing
Manufacturing has undergone numerous transformations over the years. Starting from the industrial revolution, each phase has brought new methodologies and technologies. The evolution can be notably categorized into several stages:
- Craft Production: At this stage, goods were made by skilled artisans. High customization, but low scale.
- Mass Production: Introduction of assembly lines allowed for larger quantities but with less variability in products.
- Lean Manufacturing: Focused on waste reduction and efficiency, emphasizing continuous improvement.
- Smart Manufacturing: Currently, this phase is characterized by the use of interconnected technologies to enable seamless operations.
Each phase has built upon the last, paving the way for more sophisticated methods in manufacturing. The current stage, dominated by smart factory principles, signifies a crucial shift in how industries operate, preparing them for the future.
Ericsson's Vision for Smart Factories
The modern manufacturing landscape is in a state of transformation, driven by advances in technology. Ericsson's vision for smart factories encapsulates this shift. By integrating innovative solutions, Ericsson is paving the way for a more efficient, sustainable, and adaptable manufacturing paradigm. The primary goal is to optimize production processes while maximizing resource utilization. This vision is not merely about technological prowess; it is about creating a new standard within the industry that emphasizes collaboration, agility, and intelligence.
Strategic Goals and Objectives
Ericsson’s strategic goals in developing smart factories are clear. They aim to enhance operational efficiency, improve product quality, and foster quicker market responsiveness. By employing advanced analytics and machine learning, Ericsson wants to facilitate predictive maintenance and dynamic resource allocation.
Key objectives include:
- Implementing Internet of Things (IoT) technologies: Leveraging connected devices for real-time data collection and monitoring.
- Enhancing automation: Utilizing robotics to streamline production lines and reduce human error.
- Emphasizing sustainability: Minimizing carbon footprint through efficient energy usage and waste reduction practices.
Each of these goals supports the overarching vision of revolutionizing the manufacturing sector.
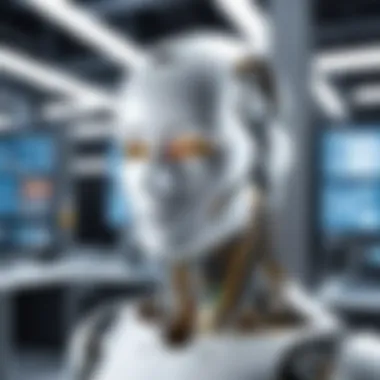
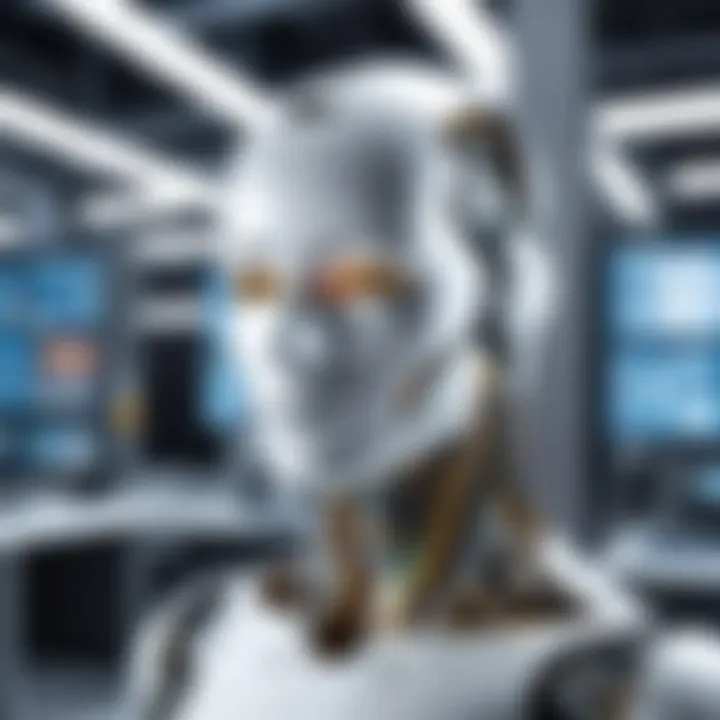
Key Components of Ericsson's Approach
Ericsson’s approach to smart manufacturing hinges on several key components that work in tandem to achieve the desired outcomes. These components include:
- IoT Integration: A cornerstone of the smart factory concept, IoT allows for the seamless exchange of data between machines and systems, fostering real-time monitoring and control. This enables factories to predict potential issues before they arise.
- Artificial Intelligence: AI plays a critical role in analyzing vast amounts of data collected from production processes. Through machine learning algorithms, the system can identify patterns, optimize workflows, and even forecast maintenance needs.
- Advanced Robotics: Automation is enhanced through the implementation of robotics, which reduces manual labor and speeds up production. These robots can work collaboratively alongside human operators, increasing overall productivity.
- Cloud-Based Solutions: Utilizing cloud computing facilitates centralized data management. This practice allows for more robust data analysis and enhances the scalability of manufacturing operations.
- Cybersecurity Measures: As factories become more connected, securing data against cyber threats is paramount. Ericsson places significant emphasis on establishing stringent cybersecurity protocols to protect sensitive information and systems.
"The future of manufacturing lies in the convergence of advanced technologies, creating synergy and efficiency."
These components, viewed together, underscore Ericsson's holistic approach to creating smart factories that not only enhance productivity but also promote sustainability and security.
Technology Behind Ericsson's Smart Factory
The efficiency and efficacy of Ericsson's Smart Factory hinge significantly on the integration of advanced technologies. These technologies are no longer merely tools; they redefine how manufacturing operates. As the manufacturing landscape evolves, companies must adapt to the incessant demands for flexibility, speed, and quality. The incorporation of key technologies like the Internet of Things (IoT), artificial intelligence (AI), machine learning (ML), and automation paves the way for a more synergistic manufacturing environment. This section delves into the specifics of these technologies, their benefits, and the broader impact they have on Ericsson's manufacturing processes.
Integration of IoT in Manufacturing
Integrating IoT in manufacturing sets the stage for real-time communication and data analysis. IoT devices collect data from machinery, products, and sensors, enabling a seamless flow of information across the production line. With this data, manufacturers can monitor processes closely and optimize operations based on real-time insights.
- Benefits of IoT Integration:
- Enhanced visibility into production operations
- Reduced downtime via predictive maintenance
- Improved supply chain coordination
By leveraging IoT, Ericsson creates a smarter factory ecosystem that can respond quickly to changing production needs and market demands. This proactive approach minimizes inefficiencies and enhances operational agility.
Role of Artificial Intelligence and Machine Learning
Artificial intelligence and machine learning are central to transforming traditional manufacturing. AI algorithms analyze large sets of data to inform decision-making processes. It can predict failures, optimize production schedules, and enhance quality control measures.
- Specific Impacts of AI and ML:
- Improved accuracy in defect detection
- Efficient resource management
- Customizability in production runs based on real-time data
These technologies foster a more intelligent manufacturing process, minimizing errors and streamlining workflows. Ericsson's application of AI and ML profoundly influences their factory performance, likely contributing to enhanced product quality.
Automation and Robotics in Production
Automation in manufacturing refers to utilizing technology to control and monitor production processes. Robotics plays a key role in achieving higher efficiency through automation. Robots can perform repetitive tasks with precision, reducing labor costs and increasing safety.
- Advantages of Automation and Robotics:
- Increased production speed and consistency
- Reduction of human error in manufacturing tasks
- Ability to operate in hazardous environments
Ericsson’s use of robotics complements its overall strategy for achieving a smart factory. These technologies not only enhance productivity but also enable higher flexibility, allowing the factory to pivot quickly in response to market shifts or demand changes.
The continued integration of IoT, AI, ML, and automation in manufacturing technologies heralds a new era of productivity and efficiency.
In summary, the technology behind Ericsson’s Smart Factory is about creating a highly efficient and adaptive manufacturing environment. Each component plays a critical role in ensuring that the factory is not just smart but also responsive to the complexities of modern production demands.
Impact on Manufacturing Efficiency
In the realm of modern production, the efficiency of manufacturing operations stands as a critical determinant of competitiveness. With the advent of smart factories, particularly those pioneered by Ericsson, the framework of manufacturing has begun to shift dramatically. Efficiency is not simply a metric but a vital element that underpins decision-making, resource allocation, and overall operational success.
The integration of advanced technologies enables manufacturers to achieve unprecedented levels of efficiency. At the heart of this transformation lies the ability to analyze data in real-time, which provides companies with insights that were previously unattainable. This not only aids in decision-making but also allows for more agile responses to market demands.
Real-time Data Analysis and Decision Making
Real-time data analysis is a cornerstone of Ericsson's smart factory paradigm. It enables the collection, processing, and analysis of vast amounts of information from multiple sources. Whether it is data from production machinery, supply chain logistics, or market trends, the ability to harness such information is essential.
Decisions made based on real-time insights can significantly reduce response times. For example, if a machine shows signs of deviation from its normal operational parameters, immediate data can trigger automatic adjustments or alerts. This leads to fewer disruptions in production. The access to real-time analytics informs managers about bottlenecks and inefficiencies, prompting timely strategic decisions.
The benefits of real-time data are multifaceted, including:
- Enhanced visibility into processes that allows for proactive management.
- Informed decision-making based on comprehensive data rather than assumptions.
- Lower operational costs through optimized resource usage.
"Manufactures can leverage real-time data for agile decision-making, thereby ensuring that operational efficiency is maximized at all times."
Reduction of Downtime and Waste
Reducing downtime is pivotal for producing at higher efficiency. Ericsson’s smart factory approach employs predictive analytics to anticipate machine failures before they occur. By utilizing data collected on equipment performance, it is possible to schedule maintenance activities at optimal times. This not only maximizes machine availability but directly impacts profitability.
Moreover, the smart factory framework emphasizes waste reduction across various dimensions. Adopting lean manufacturing principles, combined with intelligent automation, minimizes materials wastage during production. This is achieved through precise monitoring and control systems, ensuring that resources are utilized effectively.
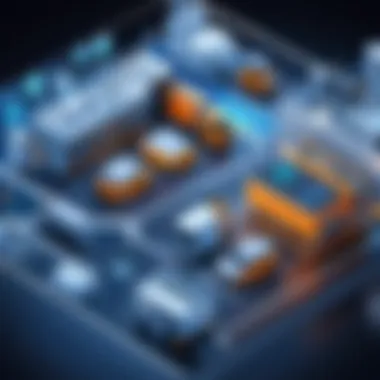
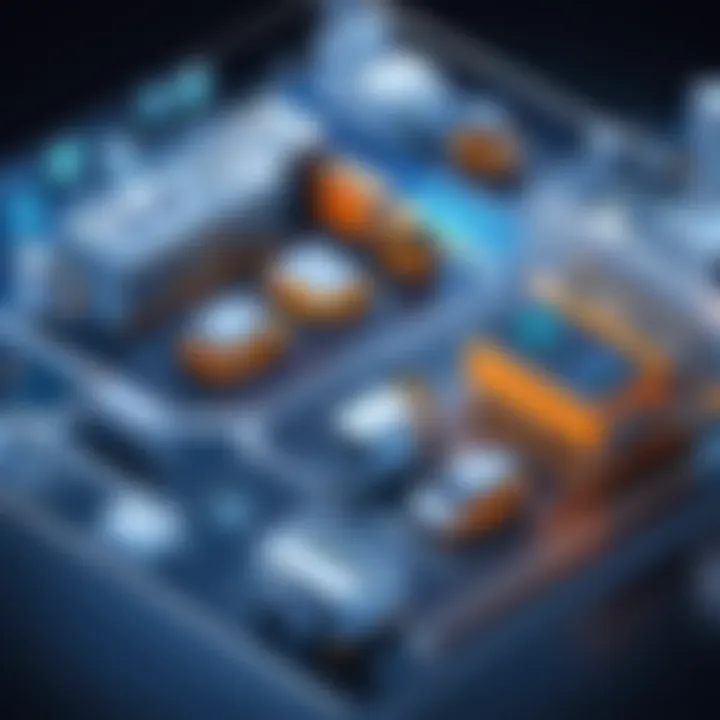
The strategies for achieving reduced downtime and waste include:
- Predictive Maintenance: Utilizing sensors and IoT devices to monitor machinery health.
- Continuous Improvement: Ongoing evaluation of processes to identify inefficiencies.
- Smart Resource Management: Optimizing inventory levels to prevent overstocking and spoilage.
Ultimately, the focus on efficiency, driven by real-time monitoring and proactive management, crystallizes the significant advantages that smart factories like Ericsson's bring to the manufacturing landscape.
Sustainability in Smart Factories
The concept of sustainability is critical in today’s manufacturing landscape. As businesses aim to minimize their environmental footprint, sustainable practices become increasingly important. Ericsson's Smart Factory exemplifies how integrating sustainability into manufacturing is not just a responsibility but also a strategic advantage.
Sustainability in smart factories encompasses various elements such as energy efficiency, waste management, and the broader acknowledgment of social responsibilities. These practices offer multiple benefits including cost savings, compliance with regulations, and improving the brand’s reputation.
Smart factories must focus on creating processes that reduce resource consumption while maintaining productivity. Implementing these sustainable initiatives can enhance operational resilience and create a more positive impact on the surrounding community and environment. The following sections will explore the specific strategies applied within Ericsson's approach to sustainability.
Energy Efficiency Initiatives
Energy efficiency is a key component of sustainability strategies in smart factories. By optimizing energy use, manufacturers can reduce costs and minimize their environmental impact. Ericsson employs several initiatives aimed at energy efficiency:
- Smart Energy Management: This system monitors and controls energy consumption across various processes in real-time. By analyzing data, the factory can adjust operations to optimize energy use without sacrificing output.
- Use of Renewable Energy: Incorporating renewable energy sources such as solar or wind reduces reliance on fossil fuels. This shift not only lowers carbon emissions but can also stabilize energy costs over time.
- Energy-efficient Equipment: Upgrading to high-efficiency machinery helps in reducing overall energy consumption. Ensuring that all equipment meets stringent energy standards is a significant step towards achieving sustainability goals.
Achieving energy efficiency requires ongoing assessment and adjustment. Ericsson’s facilities regularly track energy consumption patterns and explore new technologies that can further reduce energy reliance.
Waste Management Practices
Efficient waste management is vital in the pursuit of sustainability in smart factories. Reducing waste not only lessens the environmental burden but also contributes to cost savings. Ericsson implements effective waste management strategies:
- Zero Waste Goals: Setting ambitious targets to minimize landfill waste encourages all employees to engage in rigorous recycling and composting programs.
- Lean Manufacturing: Streamlining processes to eliminate waste in production means using fewer resources and creating less scrap. This methodology promotes a culture of efficiency.
- Material Reuse: Introducing practices that allow scrap material to be repurposed or recycled into production processes minimizes resource extraction and reduces waste.
Adopting effective waste management practices requires commitment from all levels of the organization. The involvement of employees fosters a culture of sustainability that permeates the workplace, leading to more significant environmental outcomes.
Workforce Dynamics in a Smart Factory Environment
The advent of smart factories has initiated significant changes in workforce dynamics within the manufacturing sector. As technology becomes integrated into manufacturing processes, the roles, skills, and interactions of workers evolve. This transformative era demands not only technical know-how but also adaptability and continuous learning among employees. Understanding these changes is essential for stakeholders to align their strategies with the shifting workforce requirements.
In smart factories, workers often engage with sophisticated technologies, such as automation systems and artificial intelligence. Thus, the environment requires greater collaboration between human workers and machines. This new collaboration enhances productivity and can lead to improved job satisfaction as workers take on more intellectually stimulating tasks. However, it is crucial to address potential challenges, such as fear of job displacement and the need for upskilling to work alongside advanced technologies.
Skills Required in the Modern Manufacturing Landscape
In the smart factory setting, specific skills become paramount. Workers must possess a blend of technical and soft skills to operate effectively. Key skills include:
- Technical Proficiency: Knowledge of automation, data analysis, and IoT systems.
- Analytical Thinking: Ability to interpret data and make informed decisions quickly.
- Problem-solving Skills: Navigating challenges posed by complex machinery and production processes.
- Adaptability: Willingness to learn new technologies and adjust to new job roles.
- Team Collaboration: Working as part of diverse teams to optimize production efficiency.
These skills underscore a shift from manual labor to a more knowledge-based workforce. Workers must now be equipped to respond to dynamic manufacturing needs efficiently.
Training and Development Opportunities
To equip the workforce with the necessary skills, organizations must actively invest in training and development. Opportunities can include:
- On-the-job Training: Practical experience with new technologies on the production floor.
- Workshops and Seminars: These enable workers to explore advanced topics in manufacturing technologies and best practices.
- Online Courses: Access to flexible learning options via platforms; these can deepen knowledge in specific areas such as automation or data analytics.
- Mentorship Programs: Pairing less experienced workers with seasoned professionals fosters knowledge transfer and skill development.
Through these initiatives, companies can build a workforce capable of thriving in a smart factory environment, reducing skills gaps, and enhancing overall productivity.
"Successful adaptation to smart manufacturing requires a comprehensive approach to workforce development, engaging employees in ongoing learning to meet evolving industry demands."
By focusing on workforce dynamics, organizations can ensure they are not only prepared for the challenges of modern manufacturing but also positioned to leverage the full potential of their human resources.
Challenges and Limitations
As manufacturing advances towards a more integrated and intelligent future, it is crucial to address the inherent challenges and limitations associated with smart factories. This section examines key concerns, particularly regarding cybersecurity risks and the integration of legacy systems. Understanding these challenges helps manufacturers navigate the complexities of transitioning to smart manufacturing frameworks, enabling them to harness benefits while mitigating potential setbacks.
Cybersecurity Risks in Smart Manufacturing
The rise of IoT and connected systems within smart factories creates vulnerabilities that can be exploited by malicious entities. Cybersecurity transforms from a secondary consideration to a focal point in this environment. Unlike traditional factories, where physical security measures were often sufficient, smart factories face threats that can disrupt operations, compromise sensitive data, and jeopardize system integrity.
Consequently, manufacturers must prioritize robust cybersecurity frameworks. This includes implementing strong access controls, encryption, regular software updates, and continuous monitoring of network activities. Moreover, employee training is vital, as human error can often be a significant security gap.
"The emphasis on cybersecurity in smart manufacturing is not just a precaution; it is a necessity to preserve trust and reliability in automated processes."
Integration Issues with Legacy Systems
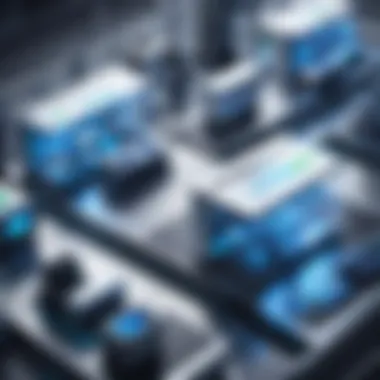
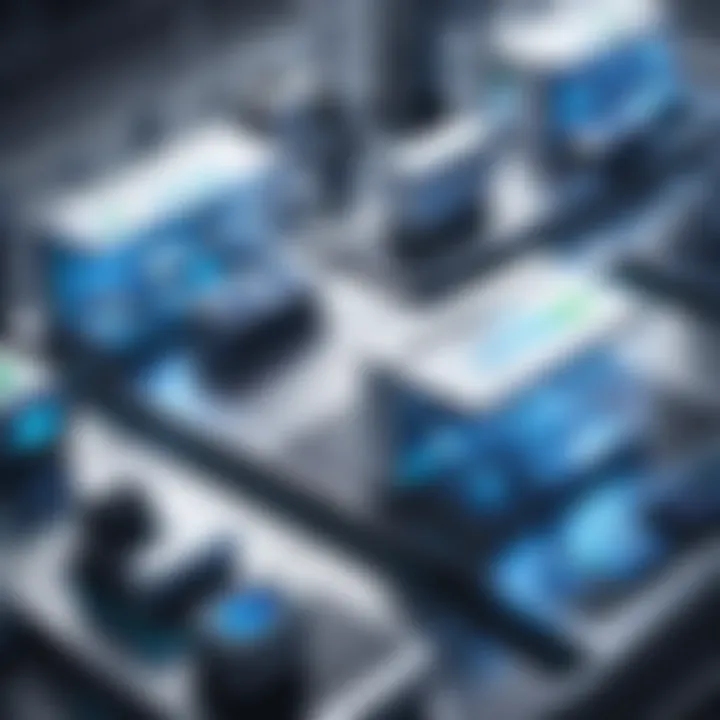
Integrating modern technologies into existing production environments presents its own challenges. Many manufacturers operate with a mix of outdated systems, which may not easily communicate with advanced technologies such as AI and IoT. This lack of compatibility can lead to inefficiencies and hinder the full realization of smart manufacturing potentials.
Testing and adaptation are essential when introducing new solutions alongside legacy systems. Manufacturers must assess the scalability of their current infrastructure and determine which elements can be upgraded, replaced, or retired. In some instances, this might involve significant investment and strategic planning to ensure a smooth transition.
Addressing integration issues requires a multifaceted approach which includes:
- Conducting thorough integration assessments to identify pain points
- Fostering collaboration between IT and operational teams
- Developing phased implementation strategies to minimize disruption
Looking Ahead: The Future of Smart Factories
The future of smart factories represents a crucial turning point in the manufacturing industry. As technologies evolve and sectors adapt, companies have to prepare for significant shifts in how production processes are conceived and executed. Understanding this landscape informs decision-making, influences investment strategies, and guides both large corporations and startups in navigating upcoming challenges and opportunities.
Adopting a forward-thinking mindset in smart manufacturing involves more than just implementing new technologies. There are essential elements to consider, including scalability, adaptability, and sustainable practices. Future factories must be designed with flexibility, allowing for easier adjustments to new trends, demands, or shifts in market dynamics. By focusing on these aspects, businesses can aim for durable growth and resilience against potential disruptions.
Beyond the tangible technologies, the way people and machines work together will evolve. The integration of smart technologies into the workplace will significantly enhance employee productivity and satisfaction. Workers will increasingly be equipped with tools that enable them to make informed decisions, relying heavily on data analytics and artificial intelligence.
"The integration of human agents with smart technologies will redefine conventional roles within the workforce, marrying technical finesse with domain knowledge."
Innovations on the Horizon
The smart factories of the future will leverage several innovations shaping the manufacturing landscape. These include advancements in robotics, additive manufacturing, and advanced analytics tools. The rise of collaborative robotics, or cobots, which work alongside humans, enhances the efficiency of assembly lines while allowing for higher safety standards. These robots can learn from human workers, improving over time and adapting to specific tasks.
Additive manufacturing, often referred to as 3D printing, will continue to transform production methods. This technology allows for rapid prototyping and the ability to produce highly customized products at scale, reducing waste and minimizing inventory costs. As this methodology becomes more mainstream, we may observe a shift toward localized production, which can be more responsive to consumer needs.
Advanced analytics tools harness big data to drive decision-making. By analyzing patterns and insights from operational data, factories can forecast demand more accurately, optimize their supply chains, and perform predictive maintenance on machinery. The result is a more efficient workflow, reduced operational costs, and a stronger competitive edge.
The Role of Collaborations and Partnerships
Collaborations and partnerships are fundamental to advancing the smart factory paradigm. As technologies become more sophisticated, no single entity possesses all the expertise necessary to drive innovation. Hence, cross-industry collaborations can lead to groundbreaking solutions. For example, partnerships between tech companies and traditional manufacturers can enhance the capabilities of production systems by integrating IoT and AI.
Furthermore, engaging with startups can provide established manufacturers with fresh insights into agile practices and innovative solutions. These collaborations can yield significant advantages, including speeding up the innovation cycles and improving scalability.
Managing these partnerships requires a strategic approach. Companies must identify the right allies whose technological direction aligns with their own goals. Effective communication and shared objectives will be essential in fostering productive relationships.
In summary, the future of smart factories is bright, but it demands careful planning and implementation. By focusing on adopting innovative solutions and fostering collaborations, businesses can stay ahead of the curve, positioning themselves for success in an ever-evolving manufacturing landscape.
Case Studies and Real-World Examples
Case studies serve a critical function in understanding the practical implications of Ericsson's smart factory initiatives. These real-world examples demonstrate how theoretical concepts translate into tangible results within manufacturing operations. By examining specific instances, readers can see the real impacts of smart technologies on production efficiency, workforce adaptability, and sustainability measures.
Successful implementations provide detailed insights into strategies, challenges, and outcomes. They highlight how various technologies integrate and adapt within distinct environments and showcase the scalability of solutions tailored for diverse operational needs.
Successful Implementations of Smart Factories
Ericsson has undertaken several projects that exemplify successful applications of smart factory concepts. One notable example is the smart factory established in Lewisville, Texas. This facility utilizes advanced automation technologies paired with data analytics capabilities to enhance operational efficiency. The integration of the Internet of Things (IoT) enables the factory to collect vast amounts of data in real-time. This data informs decision-making, optimizes workflows, and minimizes production delays.
Additionally, Ericsson's facility in Lewisville also focuses on sustainability. By implementing energy-efficient practices and materials management solutions, this factory not only boosts its productivity but also reduces its environmental footprint. Workers in this facility benefit from enhanced training programs that familiarize them with new technologies and processes, fostering a progressive work environment where continuous learning is encouraged.
Lessons Learned from Ericsson's Initiatives
Lessons gleaned from Ericsson's initiatives offer valuable insights for manufacturers looking to enhance their operations. One primary lesson is the importance of continuous innovation and adaptation. Technology evolves rapidly, and factories must embrace an agile mindset to keep pace with changes in the market and consumer demands. Emphasizing a culture of flexibility can significantly enhance operational resilience.
Another significant lesson is the necessity of investing in workforce development. Training programs should not only teach new technical skills but also prepare employees to work alongside advanced technologies such as artificial intelligence and robotics. This investment in human capital ensures that the workforce is equipped to maximize the potential of smart manufacturing.
Lastly, the case studies underline the significance of collaborative partnerships. Collaborations with technology providers, research institutions, and industry peers can drive innovation and create shared learning environments. These alliances facilitate the exchange of ideas and best practices, which can accelerate the journey to a fully integrated smart factory environment.
Successful implementations of smart factories provide real insights into challenges and solutions, shaping the future landscape of manufacturing.
Closure
The discussion surrounding Ericsson's Smart Factory is significant. This article highlights how innovative technologies are reshaping the manufacturing industry. Understanding Ericsson's approach helps illuminate the broader trends affecting global manufacturing. Manufacturers must adapt to the ongoing transformation to stay competitive.
Summary of Insights
Ericsson's Smart Factory exemplifies modern manufacturing principles. The integration of IoT, AI, and robotics creates a sophisticated production ecosystem.
Some core insights include:
- Increased efficiency through automation.
- Improved decision-making from real-time data analytics.
- Enhanced sustainability initiatives addressing energy use and waste management.
These elements collectively contribute to a more agile and resilient manufacturing sector. The emphasis on workforce dynamics is equally notable. It underscores the need for skilled labor adept at navigating the complex technologies involved in smart manufacturing.
Final Thoughts on the Future of Manufacturing
The future of manufacturing will be heavily influenced by the principles established in Ericsson's Smart Factory. Companies that embrace similar technologies will likely thrive. However, the adoption must be strategic, and tailored to specific industry needs.
Collaboration between manufacturers and technology providers is imperative. Ongoing innovation is essential to overcome existing challenges such as cybersecurity risks and the integration of legacy systems with new technologies.
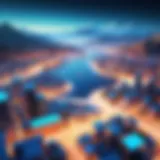
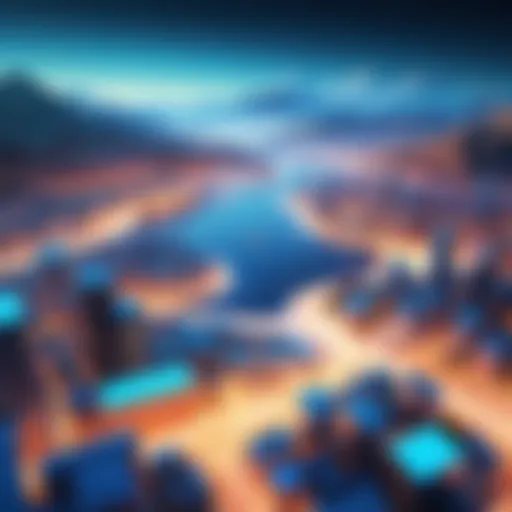