Exploring the Versatility of Onyx 3D Print Material
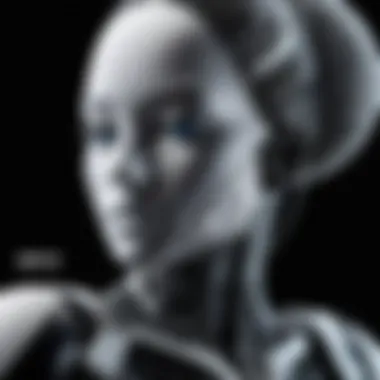
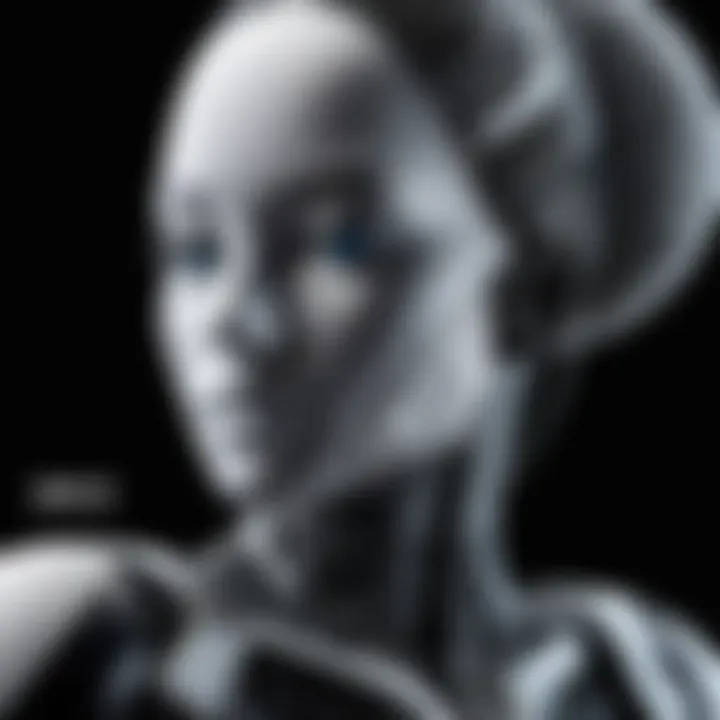
Intro
Onyx is becoming a significant player in the world of additive manufacturing. This versatile material combines nylon with microcarbon fibers. Such a blend gives onyx unique properties that are valuable in various applications. Understanding onyx's role within the 3D printing landscape is essential for tech enthusiasts and professionals alike. The exploration of onyx will cover its composition, advantages, and real-world use cases.
Latest Technological Innovations
The landscape of 3D printing is always evolving, and onyx materials are at the forefront of this technological revolution. Innovations in material science have led to new formulations of onyx that enhance its performance. Research focuses on improving the strength and flexibility while reducing print time. New techniques in 3D printing enable finer detail and smoother finishes, which further enhance the applications for onyx.
Advancements in techniques like continuous fiber fabrication contribute significantly as well. They allow for stronger parts to be printed directly from onyx composites, creating objects that meet rigorous quality standards across industries.
"The integration of carbon fiber into onyx drastically increases its impact resistance and durability, making it suitable for more demanding applications."
Applications of Onyx 3D Printing
Onyx is utilized across various industries due to its unique properties. Here are some key sectors:
- Aerospace: Onyx parts are lightweight and durable, which is crucial in aerospace applications. The material can withstand harsh environmental conditions, making it ideal for aircraft components.
- Automotive: The automotive sector also benefits from onyx. Prototypes and functional parts can be printed quickly, minimizing production time and costs.
- Medical: Custom prosthetics and surgical tools made from onyx show promise due to their lightweight nature and fine detail. This lends itself to serious medical applications where precision is key.
Advantages of Onyx
Onyx offers several advantages that make it appealing in the realm of 3D printing:
- Strength: The material is known for its excellent tensile strength, making it suitable for functional components.
- Dimensional Stability: Onyx parts maintain their shape under varying conditions, which is critical in precise applications.
- Ease of Printing: Being user-friendly, onyx works well with most 3D printers without requiring complex setups.
Environmental Impact of Onyx Materials
A key consideration is the environmental impact of using onyx. The production processes are often more sustainable than traditional manufacturing methods. Using onyx can reduce waste and energy consumption through efficient additive processes. Understanding these impacts can guide companies in making sustainable choices in their material selection.
The End
The exploration of onyx highlights its role in modern 3D printing. As we look to the future, the interplay between materials like onyx and technological advances promises intriguing possibilities. This combination is set to shape the additive manufacturing landscape for years to come.
Preface to Onyx 3D Print Material
Onyx 3D print material stands as a notable player within the expansive realm of additive manufacturing. It combines the advantages of traditional plastics with enhanced durability, making it a choice material for many creators and engineers. Understanding Onyx is critical, especially as industries seek efficient and versatile materials to meet their dynamic needs.
Primarily, Onyx is a nylon-based thermoplastic. It integrates carbon fibers, which impart significant mechanical properties to the finished prints. These enhancements address a sharp demand for stronger, lighter parts in sectors ranging from aerospace to automotive. By utilizing Onyx, manufacturers can produce components that not only function well but also have the aesthetic appeal that many products require today.
In recent years, the use of Onyx has surged. Its strength-to-weight ratio positions it favorably against other common 3D printing materials. For instance, while traditional plastics like polylactic acid (PLA) are often praised for ease of use, they lack the robustness that Onyx provides. The capabilities of Onyx enable it to support more intricate designs and applications without compromising quality.
Key Benefits
- Durability: Onyx offers superior resistance to mechanical stress, making it ideal for demanding applications.
- Aesthetic Quality: The final prints exhibit a fine surface finish, appealing for consumer components.
- Lightweight: This property is crucial in industries that require minimal weight without sacrificing strength and functionality.
Ultimately, the exploration of Onyx 3D print material reveals an exciting opportunity for innovate manufacturing practices. As we move forward, grasping the composition, properties, and applications of this material will be vital for those engaged in the tech industry, startups, and product design. They must consider Onyx not just as a material but as a means to enhance overall product capabilities.
Composition of Onyx
Understanding the composition of Onyx is crucial for comprehending its capabilities and applications in 3D printing. Onyx is a composite material that uniquely blends a polymer base with carbon fiber additives. This combination results in a material that offers exceptional strength and durability, making it particularly advantageous in various industrial settings. By analyzing the individual components of Onyx, we can appreciate its benefits and the considerations that users need to take into account when utilizing it for 3D printing.
Polymer Base
The polymer base of Onyx typically consists of nylon, a versatile and widely used material in additive manufacturing. Nylon is known for its resilience and ability to withstand significant stress and strain without deforming. This characteristic is vital for applications requiring high performance. The flexibility of nylon also enhances the overall toughness of the Onyx material, allowing for a finer range of usability in various sectors.
Moreover, the polymer's natural properties lend themselves to effective processing during the 3D printing stage. It adheres well in layers, which is critical for creating robust models. However, it is important to note that as a nylon-based product, Onyx may absorb moisture from the environment, potentially affecting print quality. Users should store the filament properly to mitigate this issue.
Carbon Fiber Additives
One of the standout features of Onyx is its integration of carbon fiber additives. These fibers reinforce the polymer matrix, significantly enhancing the mechanical properties of the material. The inclusion of carbon fiber results in a higher strength-to-weight ratio, meaning Onyx prints can be both lightweight and incredibly strong. This characteristic is particularly appealing for industries such as aerospace and automotive, where performance and weight savings are crucial.
Additionally, the carbon fiber additives contribute to Onyx's thermal stability and surface finish quality. The material is less prone to warping during the printing process than many traditional polymers. However, it also presents unique challenges. For instance, the abrasive nature of carbon fibers can cause wear and tear on standard 3D printer nozzles, necessitating the use of specialized tooling to maintain print accuracy and quality.
Overall, the composition of Onyx—combining nylon for flexibility and carbon fiber for strength—positions it as a significant player in the realm of advanced 3D printing materials. Its specific properties must be considered carefully, alongside other factors, to fully leverage its potential in various applications.
Properties of Onyx
Understanding the properties of Onyx is vital for anyone who wishes to utilize this 3D print material effectively. Its unique characteristics offer advantages that are appealing across various sectors, including aerospace, automotive, and consumer industries. Analyzing the mechanical strength, thermal stability, and surface finish of Onyx gives insights into its capabilities and limitations. This section breaks down these important properties, explaining how they contribute to the material's effectiveness in additive manufacturing.
Mechanical Strength
Onyx is known for its impressive mechanical strength, making it a preferred choice for functional prototypes and production parts. Its base polymer is combined with carbon fiber, resulting in a material that boasts enhanced rigidity. This strength is important for components that must endure significant force or pressure, such as in aerospace applications. Onyx can withstand various stresses without deforming, which makes it suitable for demanding environments.
Typically, the tensile strength reaches over 40 MPa, which is notable compared to many other 3D printing materials. This strength-to-weight ratio is particularly valuable, enabling engineers to create lighter parts without sacrificing structural integrity. Consequently, Onyx is often used in the manufacture of end-use components, where reliability is paramount.
Thermal Stability
Thermal stability is another key property of Onyx. It can maintain its performance under high temperatures, with a glass transition temperature around 90 degrees Celsius. This aspect is particularly important for applications that require exposure to variable thermal conditions. For instance, in automotive manufacturing, components may be subject to heat generated by engines. Onyx's resistance to warping or weakening under heat makes it an excellent choice for these types of applications.
Additionally, the thermal stability of Onyx facilitates better layer adhesion during printing. This results in fewer defects and reduces the likelihood of print failures, leading to a smoother production process. By understanding this characteristic, users can optimize their printing settings to achieve the best possible results.
Surface Finish
The surface finish of Onyx is commendable, allowing for a smooth, aesthetically pleasing appearance. The fine texture achieved during the 3D printing process means that post-processing is often minimized. This is advantageous for industries that prioritize cosmetic quality, as it can significantly reduce the time and cost associated with finishing parts.
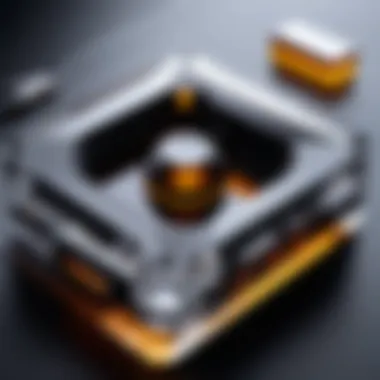
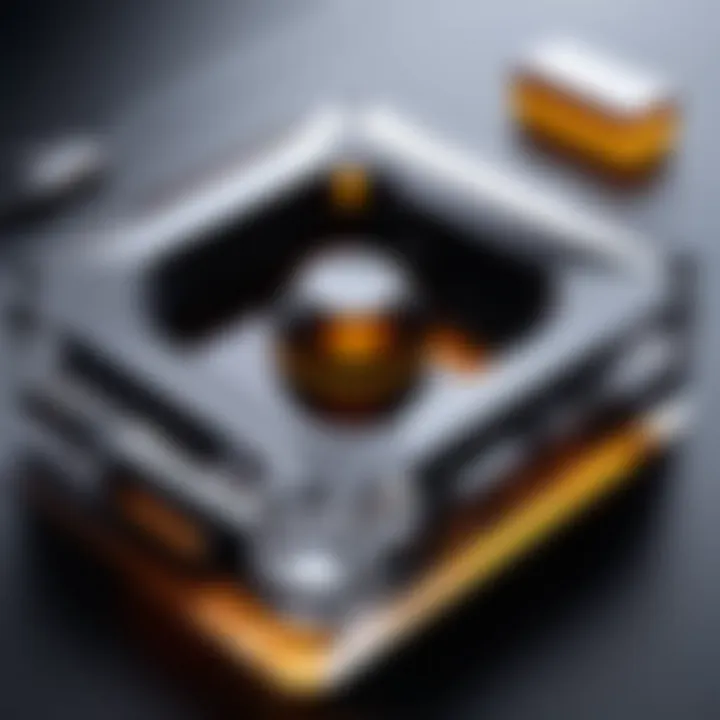
Furthermore, Onyx is receptive to additional treatments like sanding or painting. When post-processed, the surface can achieve a high-quality finish suitable for product displays or customer-facing applications. With Onyx, it's possible to balance functionality with visual appeal, enhancing the overall user experience.
In summary, Onyx’s mechanical strength, thermal stability, and superior surface finish make it an outstanding material for a variety of high-performance applications. These properties enable manufacturers to push the boundaries of what’s possible with 3D printing.
Applications of Onyx in Industry
Onyx, a versatile composite material, is making waves in various industrial sectors. Its unique properties enable it to be utilized in applications including aerospace manufacturing, automotive industry, and consumer products. Each of these sectors benefits significantly from the strength and durability of Onyx, making it a popular choice among manufacturers.
Aerospace Manufacturing
The aerospace industry is particularly demanding when it comes to materials. Onyx stands out due to its high strength-to-weight ratio, which is vital in aerospace applications. This material is extensively used for producing components that require structural integrity without the burden of excessive weight.
In aerospace, reducing weight can lead to substantial cost savings and improved fuel efficiency. Using Onyx allows engineers to create lightweight parts, like housings and brackets, that meet stringent safety standards. This is important not only for passenger aircraft but also for drones and spacecraft. The capability to manufacture custom parts using Onyx simplifies the supply chain.
Automotive Industry
Within the automotive sector, Onyx offers significant advantages in producing prototype parts. This allows manufacturers to test designs without committing to traditional production methods. The strong and durable nature of Onyx ensures that these prototypes can withstand the rigors of real-world testing conditions.
Moreover, Onyx can be utilized for end-use parts in vehicles, such as interior fittings and components that require aesthetic appeal alongside functionality. As the automotive industry shifts towards electric vehicles, manufacturers are looking for materials that can contribute to the reduction of weight while maintaining safety and performance. Onyx fits this role well, allowing for innovative design possibilities.
Consumer Products
Consumer products often demand both functionality and aesthetic appeal. Here, Onyx proves itself as an excellent material choice. The ability to create finely detailed components that are strong and attractive makes Onyx popular in the production of various consumer goods, ranging from household items to technical gadgets.
In addition to its physical properties, Onyx also allows for customization in design. This feature appeals to both manufacturers and consumers seeking unique products. Products made from Onyx are not only functional; they demonstrate a modern aesthetic that aligns well with contemporary design philosophies.
"Onyx’s versatility in 3D printing enables innovation across diverse industries, changing the way products are designed and manufactured."
In summary, the applications of Onyx in various industries are both wide-ranging and impactful. Its strength, durability, and design flexibility make it an outstanding choice for aerospace manufacturing, automotive production, and the creation of consumer products. As industries continue to evolve, Onyx is poised to play a pivotal role in shaping the future of manufacturing.
Advantages of Using Onyx
Onyx as a 3D print material offers distinct advantages that make it a noteworthy choice in the additive manufacturing sector. This section elaborates on significant benefits, focusing specifically on three key factors: strength-to-weight ratio, cost-effectiveness, and versatility in design. Understanding these advantages is essential for engineers, designers, and manufacturers aiming to optimize their projects with advanced materials.
Strength-to-Weight Ratio
One of the hallmark features of Onyx is its exceptional strength-to-weight ratio. This means that Onyx parts can bear considerable loads while remaining light. The incorporation of carbon fiber increases the stiffness and strength of the printed parts. This aspect is particularly advantageous in industries such as aerospace and automotive, where reducing weight can lead to improved performance and fuel efficiency. Furthermore, the lightweight nature of Onyx components does not compromise their durability, ensuring long-term use without failure.
When comparing materials, Onyx stands out vividly. Its ability to outperform traditional plastics like PLA or ABS, particularly under stress and heavy loads, has made it a preferred choice in demanding environments. Engineers often prioritize this feature when designing components that demand both strength and minimal weight.
Cost-Effectiveness
Another crucial advantage of Onyx is its cost-effectiveness. While the initial investment in Onyx may be higher than standard filament materials, the return on investment can be significant. The durability and longevity of parts made from Onyx lead to lower maintenance costs and reduced failure rates. This advantage is invaluable in industries where downtime translates to loss of productivity and revenue.
Moreover, the efficient use of Onyx during the 3D printing process allows for less waste and more accurate builds. This is crucial in settings where maximizing material usage is important for cost management. In addition, many manufacturers find Onyx’s compatibility with affordable 3D printers to be an added incentive.
Versatility in Design
Finally, Onyx exhibits versatility in design, making it suitable for a wide range of applications. The material can be used to create complex geometries that would be challenging to achieve with other materials. This is particularly beneficial in custom manufacturing, where tailored solutions are necessary.
Designers appreciate that Onyx can be printed in various forms, including functional prototypes and end-use parts. The ability to combine it with other materials further enhances its application potential. The flexibility in design can serve multiple sectors, from consumer products to industrial parts, offering designers the freedom to innovate without significant limitations.
"Onyx enables the production of intricate and durable components, underlining its role as a material of choice for modern creators."
In sum, the advantages of Onyx 3D print material extend far beyond its basic properties. Its strength-to-weight ratio, cost-effectiveness, and versatility make it a smart choice for anyone looking to leverage the full potential of additive manufacturing.
Comparing Onyx with Other 3D Print Materials
In the diverse landscape of 3D printing, material selection plays a crucial role in the final output. Comparing Onyx with other 3D print materials illuminates its unique features and advantages. This section examines Onyx alongside popular materials like PLA, ABS, and nylon, as well as carbon fiber composites. It’s important to detail how Onyx stands out to help users make informed decisions for their specific applications.
PLA and ABS Comparison
PLA (Polylactic Acid) and ABS (Acrylonitrile Butadiene Styrene) are two of the most commonly used 3D printing materials. Each has its characteristics, making them suitable for different tasks.
PLA is known for being easy to print, biodegradable, and having a lower melting point. However, its mechanical properties are often not as robust as Onyx. It is not ideal for high-stress applications where durability is essential.
ABS, on the other hand, offers superior strength and is more resilient to impact. Yet, it can be challenging to print because of warping and requires specific settings.
When compared to Onyx, both PLA and ABS fall short in terms of strength-to-weight ratio and thermal stability. Onyx combines a nylon base with carbon fiber, significantly enhancing its mechanical properties. This makes Onyx a preferred option for applications that demand strength and robustness, surpassing both PLA and ABS.
Nylon vs. Onyx
Nylon is a versatile polymer used frequently in 3D printing because of its strength and flexibility. When comparing it to Onyx, it is important to note one key difference: additives. While nylon performs well under various conditions, Onyx benefits from carbon fiber reinforcement.
This additive results in a material that is not only stronger but also stiffer than nylon alone. As a result, Onyx can retain its integrity under stress much better than pure nylon. Furthermore, Onyx has improved surface finish properties, making it more aesthetically pleasing for end-use parts.
Carbon Fiber Composites
Carbon fiber composites are known for their high strength and light weight. They are often utilized for specialized applications, particularly in aerospace and automotive industries. However, pure carbon fiber composites can be expensive and require advanced printers that handle composite materials.
Onyx offers a balanced alternative. It provides the benefits of carbon fiber without the extensive costs associated with fully composite materials. The carbon fiber in Onyx enhances its strength while keeping it cost-effective and accessible to a broader range of 3D printing users. In addition, Onyx is compatible with more printers, making it easier to incorporate into various workflows.
"Onyx blends the benefits of nylon with carbon fiber, making it a versatile choice in modern additive manufacturing."
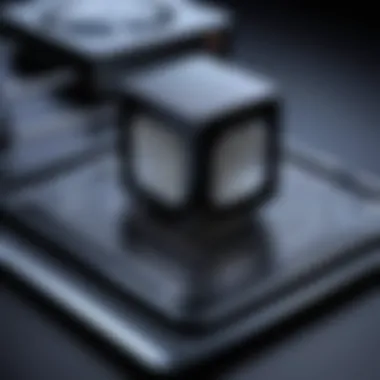
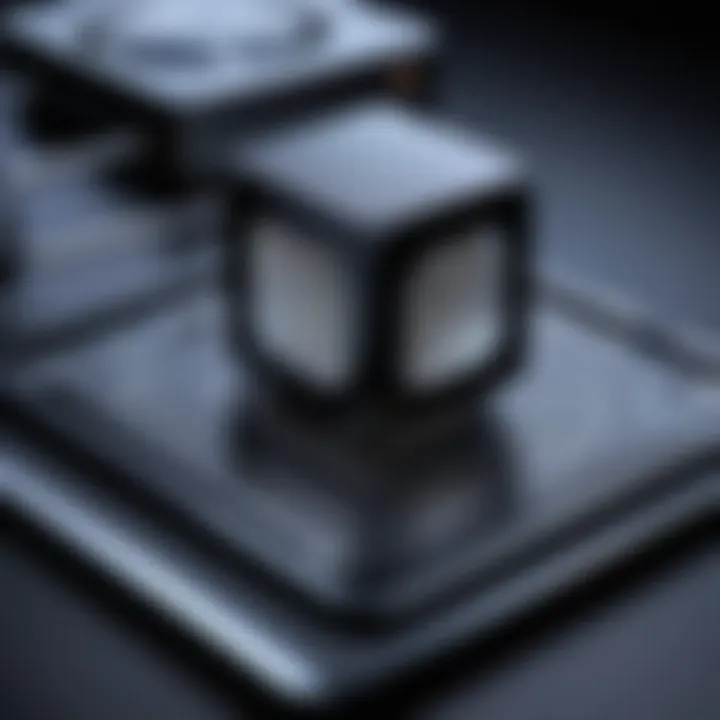
In summary, while PLA, ABS, and nylon have their strengths and weaknesses, Onyx provides a superior choice in many scenarios. Its unique composite nature offers a blend of strength, resilience, and versatility, setting a high standard in the 3D printing material market. Readers should consider these comparisons when evaluating material options to ensure the best fit for their projects.
3D Printing Process with Onyx
The 3D printing process with Onyx is a pivotal step in leveraging the material's unique properties effectively. Understanding this process enhances the application of Onyx in various industries such as aerospace, automotive, and consumer products. Getting the most out of Onyx requires attention to specific details that can make the difference between a successful print and a failed one. Despite its advantages, successful 3D printing with Onyx involves careful consideration of printing technology and settings.
Printer Compatibility
Not all 3D printers can accommodate Onyx. The compatibility primarily depends on whether the machinery can handle the specific requirements associated with Onyx. Typically, printers designed for composite materials, particularly those that support Fused Filament Fabrication (FFF) or Fused Deposition Modeling (FDM), are necessary.
Key points on printer compatibility include:
- Material Settings: The printer must be capable of reaching the correct temperature, typically around 232°C.
- Nozzle Size: A larger nozzle, often at least 0.5 mm, is recommended to ensure proper extrusion of the material.
- Build Surface: A heated bed is essential to prevent warping and to aid adhesion during the print.
Keeping compatibility in mind ensures a smoother printing process. Notably, some users report that using printers like the Markforged Onyx Pro offers a tailored experience for printing with Onyx.
Optimal Settings for Onyx
Determining optimal settings for printing with Onyx is crucial for achieving quality prints. These settings can vary based on the specific printer and environment. Start with the following baseline recommendations:
- Print Temperature: Set between 225°C and 235°C for optimal flow and layer adhesion.
- Bed Temperature: A heated bed at 60°C to 80°C helps with adhesion during printing.
- Print Speed: Slower speeds, around 30 to 50 mm/s, can significantly enhance the quality of layered construction.
- Layer Height: A layer height of 0.1 to 0.2 mm achieves finer details without sacrificing print strength.
- Cooling: Use minimal cooling for the first few layers to promote adhesion followed by moderate cooling to enhance the overall finish.
Blocks of settings can be organized as follows:
- Temperature Settings:
- Speed and Layer Height:
- Print: 225°C - 235°C
- Bed: 60°C - 80°C
- Speed: 30 mm/s - 50 mm/s
- Layer Height: 0.1 mm - 0.2 mm
Optimal settings vary based on specific use cases. Evaluate initial test prints to adjust parameters for best results.
Post-Processing Techniques
Post-processing techniques play a critical role in enhancing the quality and performance of 3D printed objects made from Onyx material. After the printing process is complete, these techniques refine the final product by improving its esthetics and functional properties. Proper post-processing helps to address surface imperfections, boosting both appearance and durability, which is crucial for applications in visually sensitive industries like aerospace and automotive.
In the context of Onyx, there are two primary post-processing techniques to consider: sanding and finishing, as well as painting and coating. Each process brings specific benefits and considerations that influence the end result of a print.
Sanding and Finishing
Sanding and finishing are essential steps in the post-processing of Onyx prints. These methods remove layer lines and other minor surface imperfections that may occur during the 3D printing process. By achieving a smoother surface, we can enhance the overall look and feel of a printed object. This is especially important in products where visual impression matters.
The sanding process typically involves the use of different grades of sandpaper, gradually moving from coarse to fine. This allows the user to effectively minimize the appearance of print lines. However, it’s essential to monitor the material closely, as excessive sanding can lead to a reduction in structural integrity.
Finishing techniques may include polishing the surface to further improve gloss and reflectivity. It is often advisable to use specific finishing compounds suitable for Onyx to achieve the best results. This two-step process of sanding followed by finishing results in a product that is not only visually appealing but also more resistant to wear and tear.
Painting and Coating
Painting and coating serve another layer of post-processing for Onyx objects, allowing for personalization and functional enhancement. A well-selected paint or coating can protect the underlying material from environmental stressors, such as moisture and UV exposure, while also providing an aesthetic upgrade to the product.
Typically, spray paints or specialized coatings designed for plastics work best with Onyx. They adhere well and are designed to be flexible, preventing cracking that may occur if the material is subjected to stress. Before applying paint, it is crucial to prep the surface by cleaning off any dust or oils, which ensures better adhesion.
Additionally, clear coatings can be applied to add a glossy finish or to protect painted surfaces from scratches and fading. The use of coatings can significantly extend the life and usability of Onyx prints in real-world applications.
In summary, the importance of post-processing techniques cannot be overstated. Whether through sanding and finishing or painting and coating, these methods transform 3D printed Onyx objects, offering enhanced aesthetics, protection, and durability. As industries increasingly turn to sophisticated manufacturing techniques, such careful consideration of post-processing will become crucial for meeting and exceeding product expectations.
Environmental Impact of Onyx
In recent years, the environmental considerations of 3D printing materials have gained traction. As the industry evolves, the impact of raw materials used in additive manufacturing comes under scrutiny. Onyx, a composite material made from nylon and carbon fiber, is no exception.
Understanding the environmental impact of Onyx is essential for stakeholders at all levels. This includes manufacturers, designers, and end-users who might be considering its use in various applications.
Sustainability of Materials
The sustainability aspect of Onyx encapsulates several key factors that are relevant in today’s eco-conscious climate.
- Recyclability: Onyx has limited recyclability compared to more traditional materials such as PLA. This is primarily due to the carbon fiber additives that complicate the recycling process. Therefore, disposal methods become an important consideration when using Onyx.
- Resource Consumption: The production of Onyx involves resources that may have environmental costs. Understanding how these materials are sourced and their impact on ecosystems is crucial. Companies increasingly recognize the importance of ethical sourcing, which can play a role in overall sustainability.
- Energy Usage in Printing: The 3D printing process itself can be energy-intensive. However, with Onyx’s properties, such as its strength and durability, products printed from Onyx may require less material than those made from more conventional substances. This quality can potentially reduce waste in the long run.
"Sustainability in manufacturing isn't just about materials; it's also about the processes that shape them."
In summary, while Onyx holds robust advantages in mechanical properties and versatility, its environmental impact cannot be overlooked. For its continued adoption in various fields, it is vital to explore improvements in recycling, responsible sourcing, and methods that lower energy consumption in the printing process.
Future Trends in Onyx Utilization
The realm of 3D printing is rapidly evolving, and Onyx material is at the forefront of this transformation. Understanding future trends in Onyx utilization is crucial for industries looking to harness the benefits of additive manufacturing. These trends can impact production processes, material development, and ultimately, how products are designed and produced.
Innovations in Additive Manufacturing
Additive manufacturing is undergoing significant innovations that enhance the capabilities of Onyx. One key area is the development of more efficient printing technologies. New printers are emerging with advanced features that allow for faster print speeds without compromising quality. This advancement enables businesses to increase their output while reducing production time.
Moreover, the integration of artificial intelligence into printing processes is expected to improve material management. Smart algorithms can predict material wear and optimize settings accordingly. This leads to a reduction in wastage and maximizes the utilization of Onyx.
There is also ongoing research into hybrid manufacturing systems, combining 3D printing with traditional methods like CNC machining. This approach allows for the strengths of both processes to improve product features and reduce manufacturing costs. With Onyx's mechanical strength and thermal stability, the combination can lead to complex, high-performance components suitable for demanding applications.
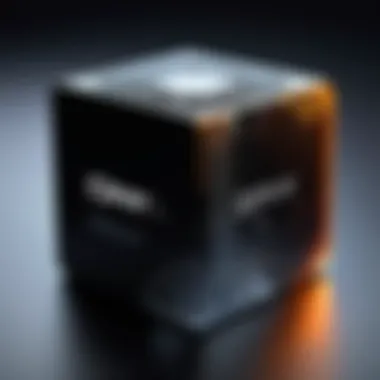
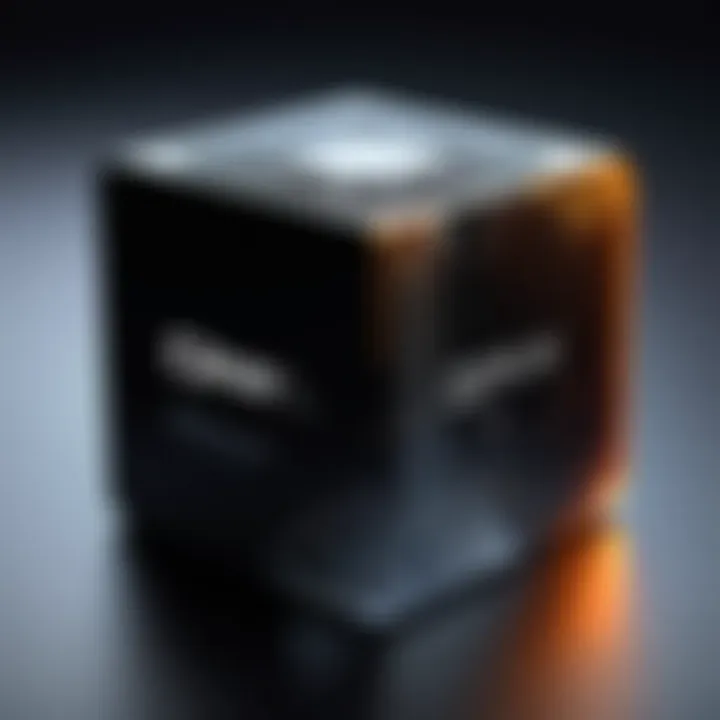
Potential New Applications
As industries continue to explore the capabilities of Onyx, potential new applications will likely emerge. One promising area is in the medical field. Custom implants and prosthetics can be designed with Onyx, incorporating individual needs and anatomical structures. The ability to create lightweight yet strong components can enhance patient outcomes and reduce recovery time.
Another area poised for growth is in aerospace. Companies are seeking to push the boundaries of lightweight materials. Onyx can enable manufacturers to produce flight components that meet the rigorous standards required in air travel, while optimizing fuel efficiency through weight reduction.
In addition, Onyx can open doors for innovative product design in the consumer sector. The blending of Onyx with other materials provides opportunities for creating unique consumer products that are both aesthetically pleasing and functional.
"The future of Onyx in 3D printing lies in its ability to adapt and evolve with emerging technologies and industry needs."
Challenges in Working with Onyx
Working with Onyx 3D print material has its notable challenges. Understanding these challenges is essential for optimal utilization of this advanced material. Though Onyx offers unique benefits, certain limitations and technical issues can arise during its application and processing. By exploring these challenges, professionals can better prepare for potential obstacles, ensuring a smoother production workflow.
Material Limitations
Onyx, primarily composed of nylon infused with carbon fiber, has material limitations that affect its use in different applications. One significant limitation is its thermal resistance. Although Onyx has better thermal stability than many alternatives, it may not withstand very high-temperature environments. This makes it less suitable for parts exposed to extreme heat.
Another limitation is material brittleness when compared to metals or pure thermoplastics. While carbon fiber enhances strength, it can also create a more brittle structure, limiting its durability in high-impact scenarios. This means parts intended for repeat stress may not perform as expected.
Additionally, Onyx can be challenging to bond with other materials. The surface may resist adhesives or coatings, affecting potential multi-material designs. This can restrict versatility in applications where material fusion is necessary. Therefore, careful consideration of the intended application is crucial when choosing Onyx.
Technical Issues in Printing
When printing with Onyx, technical issues may arise that can disrupt the workflow. One of the most common challenges is print adhesion. Onyx can sometimes struggle to adhere properly to the print bed, leading to warping or poor layer adhesion. Using a heated bed and specific adhesives can help improve this aspect, but extra setup may be needed.
The printing temperature is another technical challenge. Finding the right temperature is essential for achieving optimal results. Too low of a temperature can lead to poor layer bonding, while too high can result in excessive oozing or deformation. Calibration and experience play important roles in overcoming this issue.
"Proper calibration and setup are key to achieving high-quality prints with Onyx material."
Lastly, nozzle clogging can occur during the printing process. Carbon fiber adds reinforcement but can also contribute to wear on the nozzle. Using a hardened steel nozzle can mitigate this issue. Regular maintenance and monitoring of the printing process are essential to ensure smooth operation.
Market Outlook for Onyx 3D Printing
The market outlook for Onyx 3D printing is pivotal in understanding its present and future standing in the additive manufacturing sector. With its unique characteristics and versatile nature, Onyx attracts various industries seeking advanced materials that can enhance productivity and innovation. The analysis of current market trends and projected growth in demand highlights essential factors that affect the commercialization and adoption of Onyx materials.
Current Market Trends
Recent trends indicate a notable shift towards materials that combine strength and lightness, which is a key advantage of Onyx 3D printing. More industries are turning to this material for prototyping and end-use parts. Some current trends include:
- Customizable Applications: Onyx is increasingly utilized in both consumer and industrial applications, thanks to its adaptability. Businesses are leveraging the material's capabilities to create bespoke products tailored to specific needs.
- Sustainability Focus: As environmental concerns grow, industries favor materials with lower environmental impact. Onyx, with its sustainable properties, positions itself favorably in this changing landscape.
- Increased Adoption in Aerospace and Automotive: High performance and lightweight characteristics make Onyx suitable for demanding sectors like aerospace and automotive. This has led to a surge in use cases and investments in technologies supporting Onyx-based 3D printing.
"Additive manufacturing with materials like Onyx can significantly improve production efficiencies while maintaining robust performance standards across various applications."
Projected Growth in Onyx Demand
As industries recognize the advantages of Onyx, projections indicate sustained growth in demand. The reasons supporting this expansion include:
- Innovation in 3D Printing Technology: New developments in 3D printing technologies enhance the usability of Onyx. With continuous advancements, manufacturers can produce more complex designs while ensuring quality.
- Increased Market Awareness: As companies become more familiar with Onyx's benefits, adoption will likely rise. Educational initiatives and case studies play a significant role in informing market players.
- Expanding Industry Sectors: Beyond aerospace and automotive, sectors like healthcare and consumer goods are beginning to explore Onyx's potential. This diversification indicates a broader market for Onyx printing solutions.
In summary, the market outlook for Onyx 3D printing is optimistic, with emerging trends and projected growth showcasing its significance in the evolving landscape of additive manufacturing.
Case Studies Involving Onyx
The exploration of case studies involving Onyx 3D printing material provides practical insights into its diverse applications and effectiveness in real-world scenarios. By analyzing specific examples, readers can understand the tangible benefits and challenges associated with Onyx. These case studies serve as a testament to its capabilities, illustrating how various industries leverage this material to create innovative solutions.
Industry Success Stories
Several prominent companies have integrated Onyx into their production processes with impressive outcomes. A notable example is NASA, which has utilized Onyx for creating lightweight components essential for aerospace missions. The material's high strength-to-weight ratio allows engineers to design parts that meet stringent safety and performance standards without adding unnecessary mass. Such applications not only improve fuel efficiency but also enhance the overall mission success rate.
Another example is Ford, which applied Onyx in developing prototypes for automotive parts. By using Onyx in additive manufacturing, Ford has accelerated its prototyping process. This speed enhances their ability to test and iterate designs more effectively than traditional methods. The success of these components has led to more extensive testing and eventual use in production vehicles, showcasing the material’s reliability.
These industry success stories highlight how Onyx can deliver significant improvements in efficiency and product performance, proving its worth in competitive markets.
Innovative Uses in Startups
Startups have also embraced Onyx, finding innovative ways to utilize its properties in product development. One example is Formlabs, a startup focusing on healthcare applications. They created customized medical devices with Onyx, which allowed for rapid prototypes tailored to individual patient needs. This not only enhances patient care but also showcases the material's flexibility in meeting specific requirements.
Additionally, Laserfab, a tech startup, has explored Onyx for its unique applications in creating customized tools and fixtures for manufacturing. The company has reported improvements in machining efficiency and reduced time-to-market due to the quick iteration capabilities provided by 3D printing with Onyx.
These startups demonstrate how Onyx empowers smaller companies to compete against larger corporations by fostering innovation and accelerating product development. The benefits are clear: flexibility, efficiency, and a chance to adapt amidst rapid market changes.
"The real power of Onyx lies in its ability to transform ideas from simple sketches into functional prototypes rapidly."
Closure: The Role of Onyx in Future Manufacturing
In the fast-evolving world of additive manufacturing, Onyx has carved out a unique position. Its combination of strength, lightweight properties, and versatility makes it a formidable material for a range of industries. Manufacturers are increasingly recognizing the critical role Onyx plays in meeting the demands for high-performance parts while also considering sustainability and cost-effectiveness.
One of the significant advantages of Onyx is its strength-to-weight ratio, a critical factor in sectors like aerospace and automotive. As these industries push for lighter components without compromising strength, Onyx presents an ideal solution. Additionally, its thermal stability ensures that parts maintain integrity in environments where heat resistance is paramount.
"Onyx is set to redefine manufacturing capabilities by offering a material that not only meets but exceeds traditional performance metrics."
Future manufacturing trends indicate a growing shift towards materials that support quicker prototyping and production. Onyx is poised to play a central role in this evolution due to its fast print capabilities and versatility. It can be used for a variety of applications, from complex geometries required in consumer products, to robust functional parts in demanding environments.
However, challenges remain. Understanding the material limitations and overcoming certain technical issues during the printing process are necessary for broader adoption. Addressing these challenges will ensure that Onyx remains a viable option as technology advances.
The sustainability factor is another aspect where Onyx proves its relevance. With increasing scrutiny on the environmental impact of materials, Onyx offers a more sustainable pathway for manufacturers. As industries strive to reduce their carbon footprints, adopting materials like Onyx will be crucial.
In summation, Onyx stands out not just as another print material, but as a cornerstone in the future of manufacturing. With its unique properties, applications across different industries, and potential for innovations, it embodies the next generation of 3D print materials. Manufacturers who leverage Onyx will likely secure a competitive advantage in an increasingly complex market.